
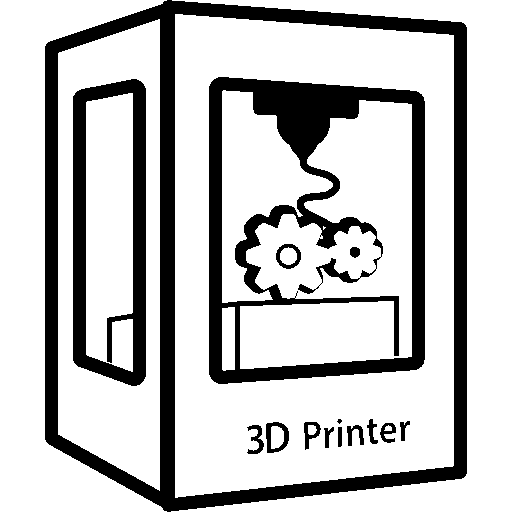
They definitely don’t know what they’re doing. They featured this one, which is a death trap. It has a disclaimer that it might not be safe above 120V, but it’s absolutely unsafe and a code violation in the US, where we use 120V (and are very litigious). The disclaimer says they’re trying to get it approved which implies they believe it could be and that the design is sound, but fundamentally it cannot meet code in the US for mains voltage use.
Even if the design were sound, there are material requirements, and having seen the quality of prints some people find acceptable, there’s no chance allowing random people online to print their own boxes is safe.
I think they basically run the contests and feature things based on “ooh this is neat” and “this will excite people to use 3d printers”. It’s a marketing thing, and I guess I accept it because I have low expectations of even pretty-good businesses. But if it’s illegal…someone should probably let them know.
This looks great! I’m super happy with my MK4, and have never had to do anything with it after the initial kit build and re-seating the LCD cable to fix some early screen-blanking issues.
I’ll probably skip this for my own printer since it seems like most (but not all) of the speed up comes from layer height, but $99 is not terrible for anyone who gets value from it. And anyone buying a new printer gets this stuff with no price increase, which is nice and makes the MK4/MK4S even easier to recommend.
I didn’t know how much more dimensionally accurate Prusa’s prints are compared to the competition, but it makes sense now why there are so many calibration models online if that just isn’t the way every printer works. I’ve designed some parts that need an 0.1mm first layer because I’ve never had any failures with that, but I guess if I share the STLs other people might have trouble.